Whether they are elastomer-metal shock absorbers or shock absorbers with assembled diaphragms, whether safety-type or not, their modelling and sizing have a non-linear behaviour. This is why their development is so complex. The issues are their lifespan and the performance of the suspended structure. In this context, the choice of elastomer and/or metal membranes, the design of the active part in silicone or another material and the calculation codes applied are all sensitive issues. GAMMA’s engineers have a wealth of knowledge and experience to draw on. Their aim is to make every project a success, synonymous with satisfaction for every customer.
The first prerequisite for this is GAMMA’s close collaboration with its customers, conducted at the earliest stage of each project. It guarantees the quality of the shock absorbers produced, and optimum control of production times and costs. To achieve these objectives, GAMMA makes the best possible recommendations to its customers, taking into account the specific constraints of each project. In addition to these standard ranges, GAMMA offers to co-develop tailor-made anti-vibration solutions. Each co-development is conducted on the basis of a 7-step process, the aim of which is to make the best technology available to the customer. In other words, the most reliable, the best performing, the most sustainable and the most innovative.
In this context, the GAMMA project manager will provide you with all the in-house resources and skills in engineering, materials formulation, prototyping and testing. This tailor-made project management is the best guarantee of achieving your objectives.
CO-DEVELOP YOUR PROJECT IN 7 STEPS
ANALYSE YOUR NEEDS
GAMMA produces and develops your shock absorbers in close partnership with you, so that we can determine the best technical compromise, taking into account your mechanical, dimensional and environmental constraints.
We parameterise the basic data for your project, considering your performance objectives in terms of filtration, stress attenuation, stability and precision, behaviour over a wide temperature range, fatigue and service life, making sure to always respect the limits in terms of stress rate.
In this context, GAMMA’s engineers are taking a close look at the following key data:
- The different types and levels of stress
- Random vibrations
- Sinusoidal vibrations
- Sine stripes on a random spectrum
- Shocks
- Shaking
- Static acceleration, combined or not
- Temperatures
- In operation
- In storage
- The desired resonance or filtration frequencies, associated with the types of stresses
- Operational life based on a defined life profile
- The geometry, available volumes and layout configuration of the suspension
- The nature of the surrounding fluids and the type of contamination, spray immersion, etc.
- The maximum possible displacement of the suspended element
- The need for a failsafe design or not
At the end of this stage, our Research Department will recommend one of the following solutions:
- produce an existing standard product that does not require tooling development, except possibly for the test phase.
- study a deviation from a standard product by adapting a specific elastomer or a particular interface according to the integration data.
- design a specific shock absorber, which will mean longer tooling development times.
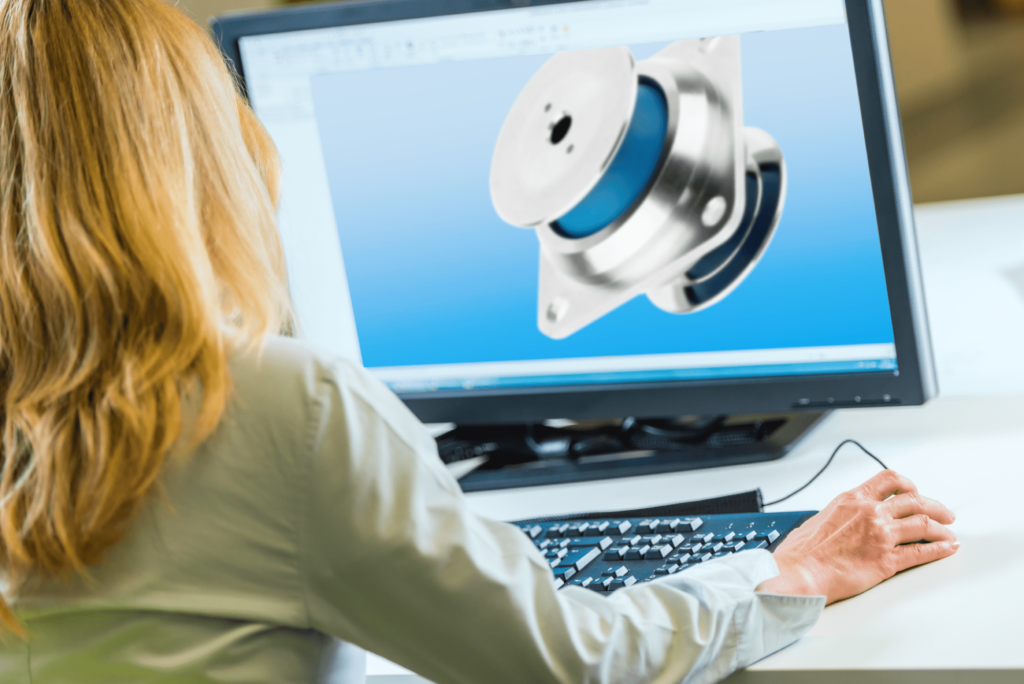
DESIGN YOUR SOLUTION
After the work in the first phase, which defined a shared and mutually accepted status of expected performance, the second, more detailed phase will begin. It will be more important if the initial conclusions lead us to recommend designing a new product.
The deliverables of this design phase are the geometry and design of the solution.
To achieve this, GAMMA’s engineers work using master curves, analytical calculations, finite element simulations, knowledge gained from our experience feedback, and any other means or tool that will enable them to exchange ideas with your teams in order to optimise your solution.
At the end of this phase, a matrix of compliance with your specifications is drawn up, committing us to developing your solution on this basis. The points not, or only partially, covered will also be specified.
We frequently offer a design review to enable you to validate the material and design of the part produced on the basis of 3D models supplied by us. The review also defines the key characteristics of future shock absorbers and the tests that will be carried out to validate them.
The shock absorbers developed can meet the requirements of the most common international standards:
- MIL-STD-810
- RTCA-DO-160
- GAM-EG-13
- STANAG
SELECT MATERIALS
When creating specific suspensions, our Development Department, which is responsible for the mechanical design of the product, works closely with our Materials Laboratory. It selects the most suitable and best performing elastomer and material for the metal part. Please note: your project may benefit from new material formulations developed by our laboratory for your most demanding applications. The Development Department also checks the fatigue strength and resistance of the entire solution, as well as its behaviour in a potentially oxidising or corrosive environment.
To ensure your project runs smoothly, our Development Department also anticipates changes in standards and REACH or RoHs regulations.
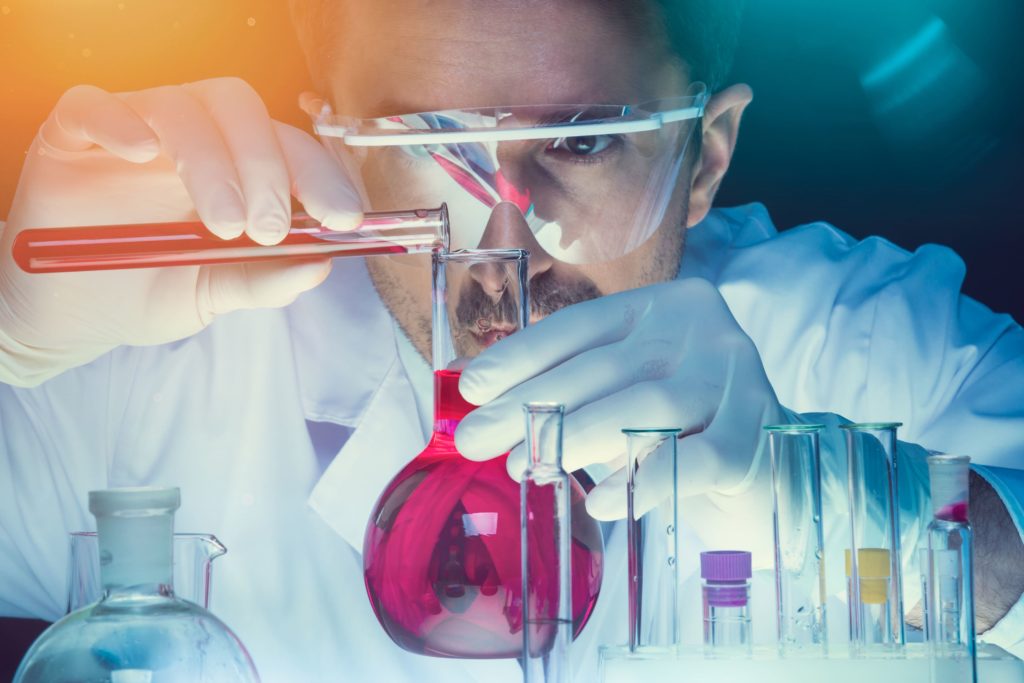
DEVELOP TOOLS
The specialists in the GAMMA Design Office develop specific moulding tools dedicated to completely new shock absorbers. Their aim is to keep subsequent iterations of fine-tuning, which would slow down development, to a minimum. The key is to ultimately design tooling adapted to the number of production cycles of future series volumes.
Depending on the project, a rapid prototyping phase using additive construction may be necessary to secure choices that are still open or, if possible, to reduce development time.
Based on the test resources and the type of test to be carried out, GAMMA produces dynamic or static test tools for future product development, qualification and series control.
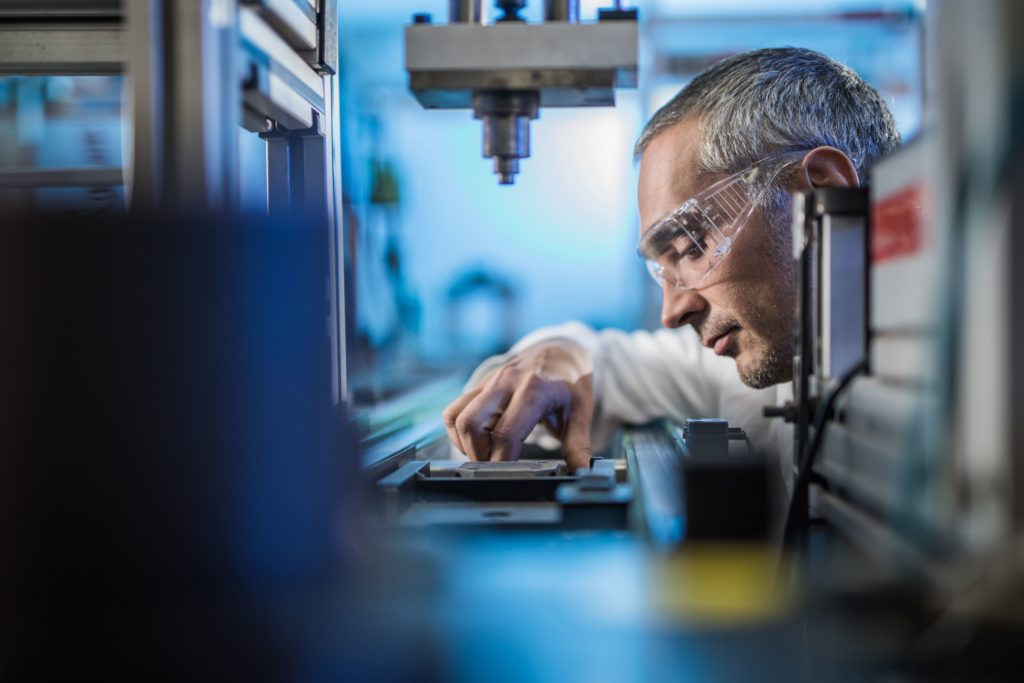
Do you have any questions?
We’ve got answers!
DEVELOP PROTOTYPES
Prototypes are produced using the same resources as for series production, to reduce the risk of drift during launch.
The parameters of each tool set-up are recorded to freeze the process and ensure subsequent traceability.
Prototype shock absorbers are made using mechanical parts in series configuration. Several types of elastomer materials are used to characterise their behaviour in the next phase of the development process.
FINE TUNE SHOCK ABSORBERS
Once all the upstream phases have been completed and approved, the shock absorbers can be fine-tuned. In the majority of cases, GAMMA opts for unit tests carried out in-house by its laboratory.
Sometimes they are followed by a validation of the behaviour of a complete suspension using 3 or even 4 shock absorbers.
GAMMA’s mechanical testing laboratory has electrodynamic excitation equipment of various capacities, which can be attached to a horizontal table to carry out tests in the 3 main axis of the shock absorbers in the real-life loading configuration. Importantly, our specialists can combine these dynamic tests with temperature-controlled tests from -50°C to +120°C. They can also simulate sinusoidal, random or combined vibration environments. Shock and vibration tests can also be carried out, as well as measuring loading characteristics as a function of the displacement applied.
Depending on the situation, GAMMA uses either accelerometric measurement chains or non-contact measurement chains using laser vibrometers. This technology eliminates the disturbances caused by the mass and position of the sensors.
After successive iterations to obtain the desired characteristics, we freeze the environment and the parameters in which the tests were carried out. We also validate the dimensional components of the suspensions developed and, where appropriate, draw up a development test report.
At this stage, a full design review is also carried out, in the form of a “first article inspection” file based on initial samples. This defines the parameters and monitoring criteria applied during the series production phase This file is submitted to our customers for prior approval.
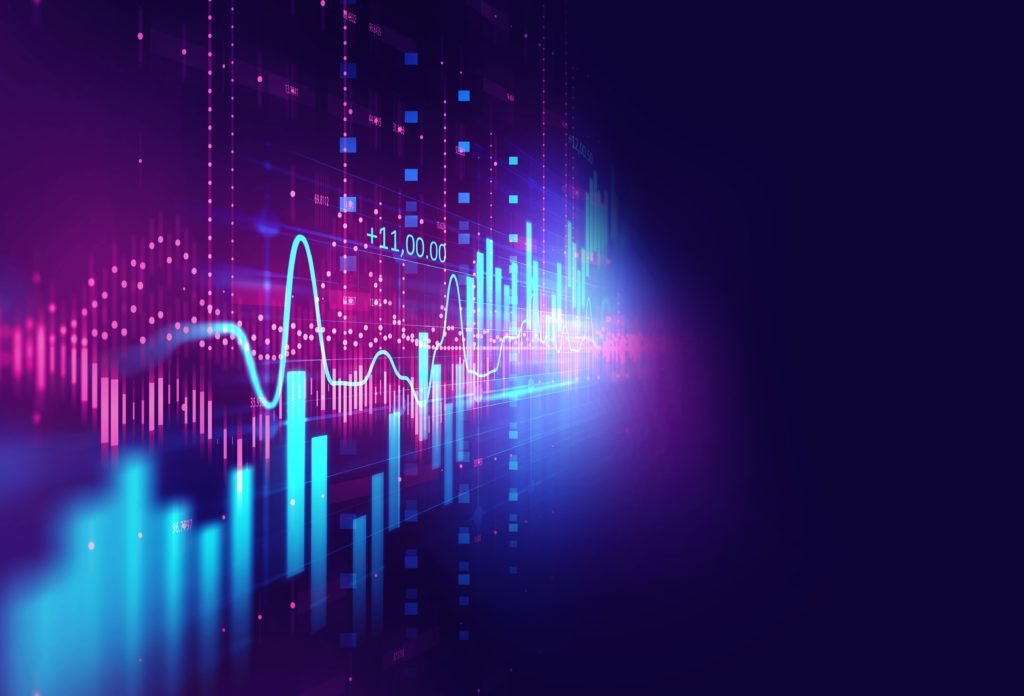
MASS PRODUCTION
Once all the phases upstream of production have been jointly decided and validated, the configuration management files will have been produced and the logistical aspects validated. From then on, series production can be launched with complete peace of mind, as they will be identical in every respect to the prototypes developed.
In the event of subsequent modifications requested by our customers or induced by changes in regulations or other factors, configuration management files will systematically be upgraded, in the form of “first item upgrade” files. In its capacity as a designer of insulation solutions, GAMMA issues these new approvals with the same high standards of interactivity, traceability and information for its customers, with special attention to the subsequent modifications made to specifically developed shock absorbers.
Do you have a project?
Don’t hesitate to discuss your project with us in complete confidentiality. We are ready to work with you to develop your ideal anti-vibration solution.