SHOCK ABSORBERS IN A FEW KEY FACTS
GAMMA’s core expertise is the development and production of high added-value shock absorbers. For us, the success of every project lies in our ongoing commitment to industrial excellence. That’s why precision, reliability, technology and innovation are key factors in our business.
- Suitable for land, sea, space and air
- High reliability: 1% performance difference in frequency and damping
- Temperature resistance: -55°C à +120°C
FIELDS OF APPLICATION
THIS EQUIPMENT INCORPORATES OUR SHOCK ABSORBERS AND ANTI-VIBRATION SOLUTIONS
GAMMA SHOCK ABSORBERS ARE SYNONYMOUS WITH VERY HIGH PRECISION IN A WIDE RANGE OF APPLICATIONS
Our applications range from the suspension of IMU navigation systems, laser gyro inertial units, fibre-optic gyro units, air data ADIRU systems, accelerometers, resonators and star pointers. GAMMA’s high-tech solutions are also incorporated into on-board optronics systems, gyrostabilized optronics balls, front-end optronics and telescopes.
These solutions can of course be used for equipment in both civil and defence aviation, for example for helicopters and drones, and in aerospace for satellites and launchers. They are also integrated into transport and drilling equipment, etc.
Wherever very high positioning accuracy, reliable guidance, resolution and image stabilisation are essential, our shock absorbers and anti-vibration solutions are the answer. Our shock absorbers are frequently failsafe-engineered and often developed using elastomers from different silicone families.
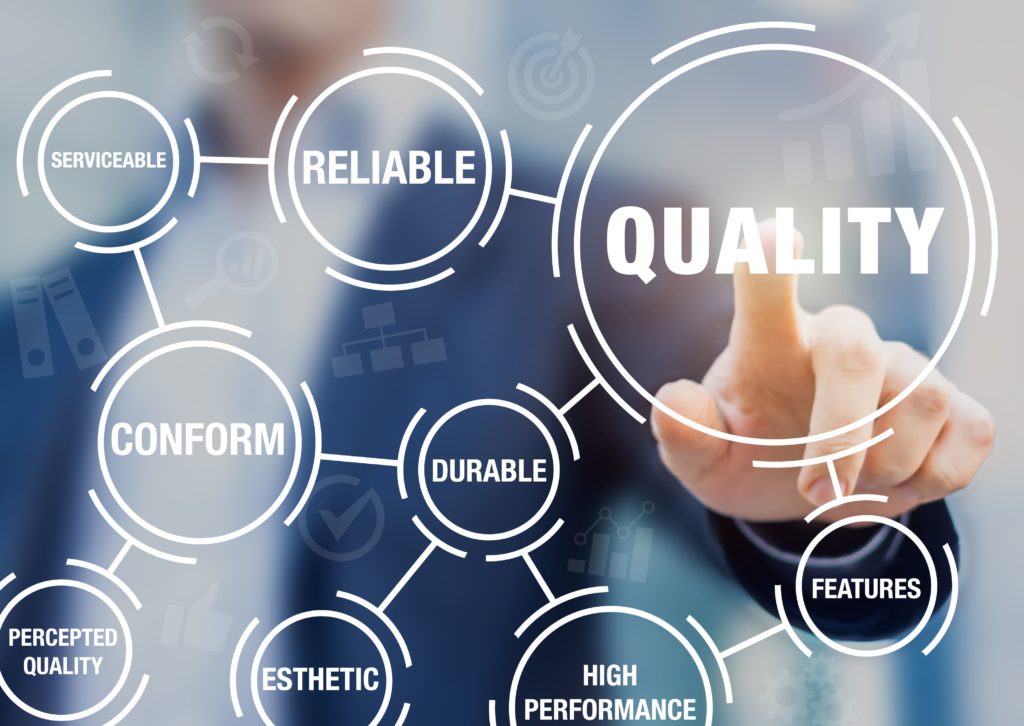
GAMMA, A RECOGNISED PARTNER IN THE DESIGN, SIMULATION AND PRODUCTION OF ANTI-VIBRATION SOLUTIONS
For over 40 years, GAMMA has enjoyed a fruitful collaboration with major players in the above-mentioned applications. In order to meet our customers’ needs as closely as possible, we frequently co-develop numerous solutions with them to optimise the performance of their products.
In this context, our extensive expertise and feedback are put to good use when it comes to designing and developing anti-vibration or anti-shock systems to protect sensitive components by attenuating vibrations, filtering high frequencies, returning to position after use, and withstanding pyrotechnic loads.
Our development processes also include simulating fatigue behaviour and estimating the service life of our solutions using numerical models. All this is crucial to the success of the projects entrusted to GAMMA.
By way of example, our engineers also consider constraints such as the frequency range, the mass and geometry of the equipment to be protected, customer interfaces and the final destination of the suspended equipment (Air, Sea, Land and Space). These constraints have a major influence on the design of the shock absorbers to be developed.
Biconical types and their derivatives are mainly suitable for Air, Sea and Land solutions. It should be noted, however, that there are other types of high-performance solutions mastered by GAMMA to develop or create highly customised shock absorber designs or others of the elastomer-metal type with high displacement capacity. This is mainly the case for marine applications.
GAMMA’s production reliability is underpinned by our ability to control characteristics in a dynamic testing laboratory. This enables us to produce very reliable suspensions with performance differences between shock absorbers of less than 1% in frequency and damping. This is how we can guarantee attenuated performance, avoid or reduce dynamic coupling and minimise deviations in return to position following severe dynamic loading.
GAMMA’s customers benefit from its global sales presence and top-level development teams, who draw on a wealth of expertise and feedback (RETEX). This is why GAMMA is able to meet all shock absorber design and manufacturing requirements within tight deadlines.
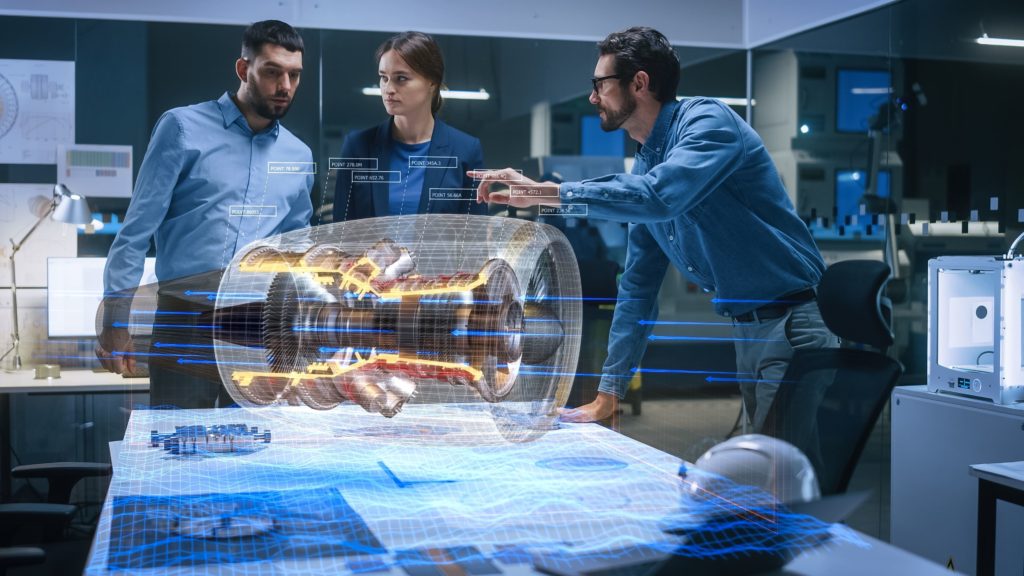
GAMMA SHOCK ABSORBERS ANTICIPATE NEW NEEDS!
GAMMA’s strategies are influenced by the imperatives of sustainable development. Whatever the case, carriers will always be powered by navigation, positioning and targeting systems. However, the reduction in onboard weight and therefore volume is irreversible. This is why they have led to a downsizing effect for the solutions offered by GAMMA.
We are now able to produce miniature shock absorbers while preserving their performance. To achieve this, we have reviewed our choice of materials, industrial processes and measurements. As a result, laser vibrometers can now be used for non-contact testing.
We also innovate by combining the mechanical properties of metallic materials with the damping properties of elastomers.
On the one hand, this combination provides even greater performance and stability, and on the other, a significant extension of the operating temperatures usually considered to be between -55°C and +120°C.
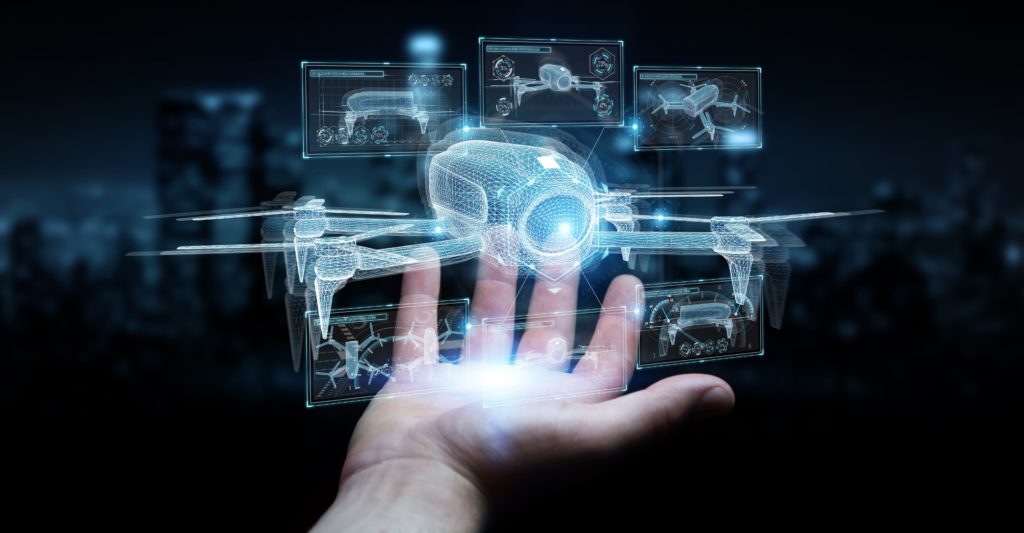
Do you have a project?
Don’t hesitate to discuss your project with us in complete confidentiality. We are ready to work with you to develop your ideal anti-vibration solution.